Protecting from the invisible killer.
Why gas detection needs to become part of your layered RPE and confined space strategy
As every risk assessor will tell you, full situational hazard awareness is an essential tool in ensuring that you can go about your work with the correct and compliant protection. But hazardous gases, in particular, are a risk that you can’t see, hear, feel and often can’t smell.
Some examples of this invisible danger:
Hydrogen Sulphide (H2S)Often produced from breakdown of organic matter in the absence of oxygen, so can be a risk in tanks, sewers, treatment plants, farming, refuse and recycling plants. The density of H2S means it tends to sink and build up at low levels. While at lower concentrations it can smell like rotten eggs, prolonged exposure means that the nose can no longer detect it.
Effects of inhalation and facial exposure range from eye irritation, sore throat and respiratory tract and shortness of breath at low concentrations, to burning eyes, corneal erosion, collapse, respiratory paralysis, convulsions, heart arrythmia and death at high concentrations. Hydrogen Sulphide is also a highly flammable gas and gas/air mixtures can be explosive. If ignited, further toxic vapours and gases may be produced. | Carbon MonoxideColourless, tasteless, odourless and non-irritating, CO is a dangerous gas which is usually produced as a by-product of the incomplete combustion of fuel. It can kill without warning – when inhaled, it attaches itself to the body’s oxygen carrier, haemoglobin, so dangerously reducing the oxygen being carried around the body. Just a brief exposure can cause flu-like symptoms - headaches, nausea, dizziness, muscle pain and personality changes. More will lead to movement problems, weakness, confusion, heart and lung problems, loss of consciousness and death. |
HSE sets a short-term exposure limit of 10 ppm for any 10-15 minute period, or 5ppm over an 8 hour period. Low alarms should be set at or below 10ppm, high alarms at or below 20ppm. | HSE sets a maximum exposure limit of 20 ppm over an 8 hour period. Physical symptoms may set in at 35ppm, but exposure to low levels over a longer period of time can still leave the sufferer with symptoms easily confused with common illnesses. |
Oxygen (O2)Leaks in pressured systems or pressure relief valves, excess oxygen used in cutting or welding processes and spills of liquid oxygen can all lead to an excess of oxygen in the environment, amongst other industrial processes.
Oxygen’s ability to accelerate burning enables materials to ignite much more easily, burning much faster and hotter in an oxygen enriched atmosphere, as can be seen with the effects of a ‘backdraft’ effect when opening a door onto an established fire.
High oxygen concentrations in inhaled air can cause inflammation and lung damage, neurological problems, vision loss, cell and tissue damage, loss of consciousness and death.
| Sulphur Dioxide (SO2)With purposes as wide as fumigation, food preservation and bleaching, the chemical SO2 is frequently used in industry, as well as being released from the burning of fossil fuels in power plants, refineries, motors and boilers. It is colourless, but with a pungent smell. Inhalation causes irritation and at higher levels, corrosion, to the respiratory tract, and similar effects to the gastrointestinal tract. Eye contact causes irritation and, in severe cases, blindness. |
Despite being essential for life, oxygen levels for regular breathing air should always be between 19.5% and 23.5%. Any lower and the air is deemed oxygen deficient, but any higher and there is the risk of both oxygen toxicity and severe fires and explosions. | HSE sets an exposure limit of 0.5 ppm over an 8-hour period but also specifies that high levels can be life threatening even with short term exposure. |
The science of making the invisible, visible.
Using a personal gas monitor allows the person entering any hazardous environment to know immediately if there are unsafe conditions. Even if they are wearing PAPR with a gas filter, or fully self-contained breathing apparatus (SCBA) it is essential to be aware of gas levels which could cause or accelerate an explosion. Sensor technologies are varied according to the substance they are aiming to detect, but generally fall under the following areas:
Catalytic
Heated wire is coated with a catalyst. Often used for combustible gases, which come into contact with the wire, burn and raise the temperature, so changing the resistance of the wire.
Infrared
Sensors emit infrared light and measure the amount absorbed by the gas. Different gases absorb infrared light at different wavelengths and this allows identification. Often used to detect Carbon Dioxide.
Electrochemical
Sensors use electrodes and a chemical reaction which produces an electrical current. The magnitude of this indicates concentration levels. Commonly used to detect CO and H2S.
Metal Oxide Semiconductor
A heated semiconductor continuously samples the surrounding air to detect gas, converts it into an electrical signal and sets an alarm off if it is over a pre-set threshold.
Molecular Property Spectrometer
A type of flammable gas sensor which can detect multiple gases simultaneously.
Some gas monitor models can transmit readings wirelessly to enable data collection and long term gas level monitoring.
Essential across multiple industries
It’s not only in the world of Oil and Gas that das monitoring is required. Gas detectors are commonly used in many settings where industrial processes may cause exposure to harmful gases. Gas monitoring is vital where hazardous materials are being stored, transported or handled, and in confined spaces where there is a risk of gas build up and gases can displace oxygen or pose a health hazard. Firefighters and emergency response personnel use gas detectors to allow them to respond appropriately. Hazardous gases are also a significant problem in laboratories, where both gas storage and gases produced as by products can be a danger and gas monitoring is a must.
How to use a Gas Monitor
Pre-Use
- Check batteries are charged where relevant.
- Check the sensor is clean and undamaged.
- Perform a bump test*. (see below)
- Zero the monitor.
During Use
- The monitor should be worn in your breathing zone, the main entry point for toxins into the body (not on a belt or worse, in a pocket). This also ensures protection against a wider range of gases, which have different densities and so may fall and pool at low levels, or rise and accumulate higher up.
- The monitor should remain uncovered to ensure both that it can perform effectively and that the alarm is audible and warning lights can be seen.
- Pay attention and respond quickly to readings, lights and alarms. On an alarm, evacuate the area immediately, before analysing the readings.
After Use
- Follow manufacture instructions for calibration. This is essential to ensure the gas monitor is recognising the correct gas levels.
- Ensure the monitor is cleaned and store it properly in a clean and dry location.
- Consider keeping an inventory record with details of regular maintenance, battery changes and condition.
*What is a bump test?
In a bump test the gas detector is exposed to a controlled concentration of gas which is higher than any alarm set points. This tests that it is responding properly and shows that both the alarm and display are working correctly.
Anchor Safety work with trusted and experienced partners, Dräger and Crowcon, to provide a comprehensive range of gas detectors to identify and warn of dangerous gas hazards:
Drager PAC 6000 and 6500 ranges
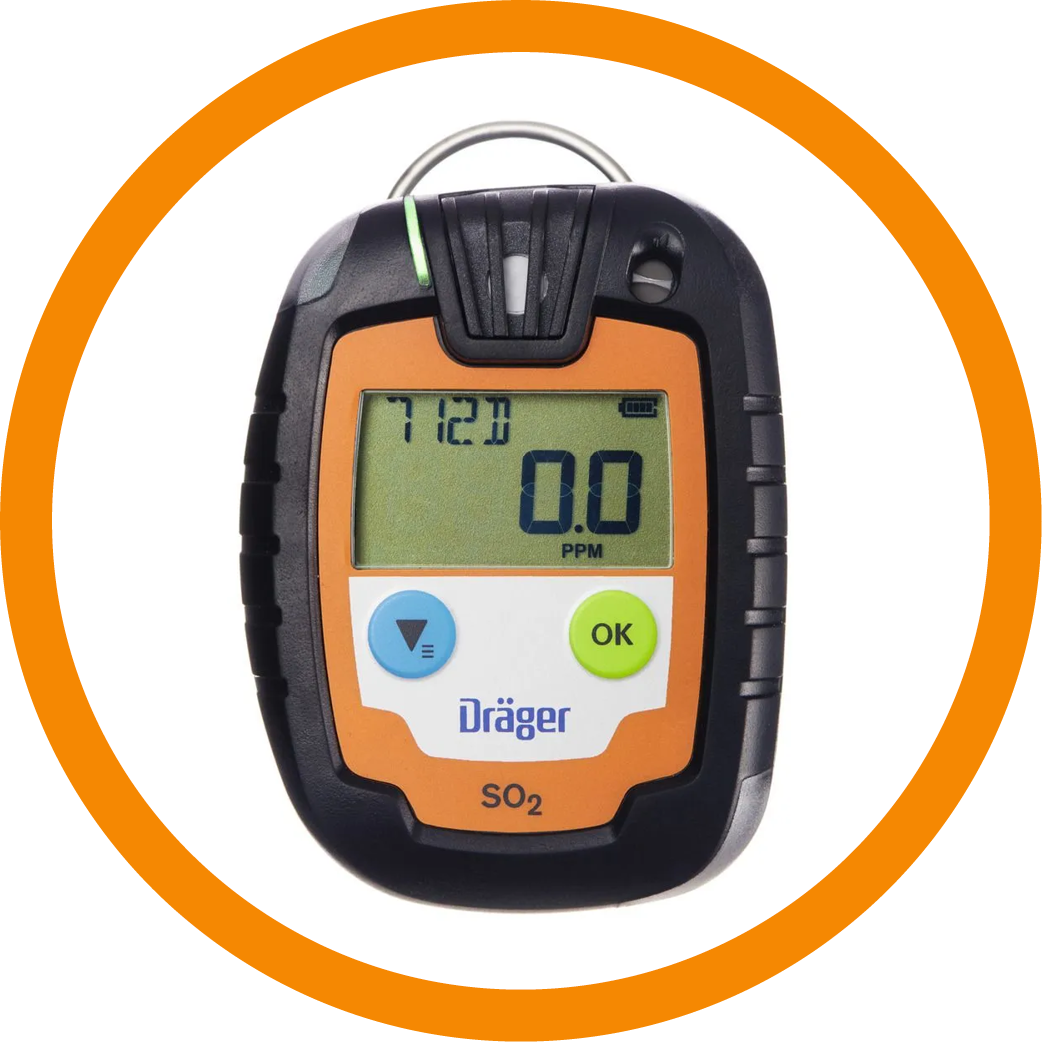
| Dräger Pac® 6000The disposable personal single-gas detection device, Dräger Pac® 6000, measures CO, H2S, SO2 or O2 reliably and precisely, even in the toughest conditions. The robust design, quick sensor response times, and a powerful battery ensure maximum safety for up to two years with virtually no maintenance required. More about the range |
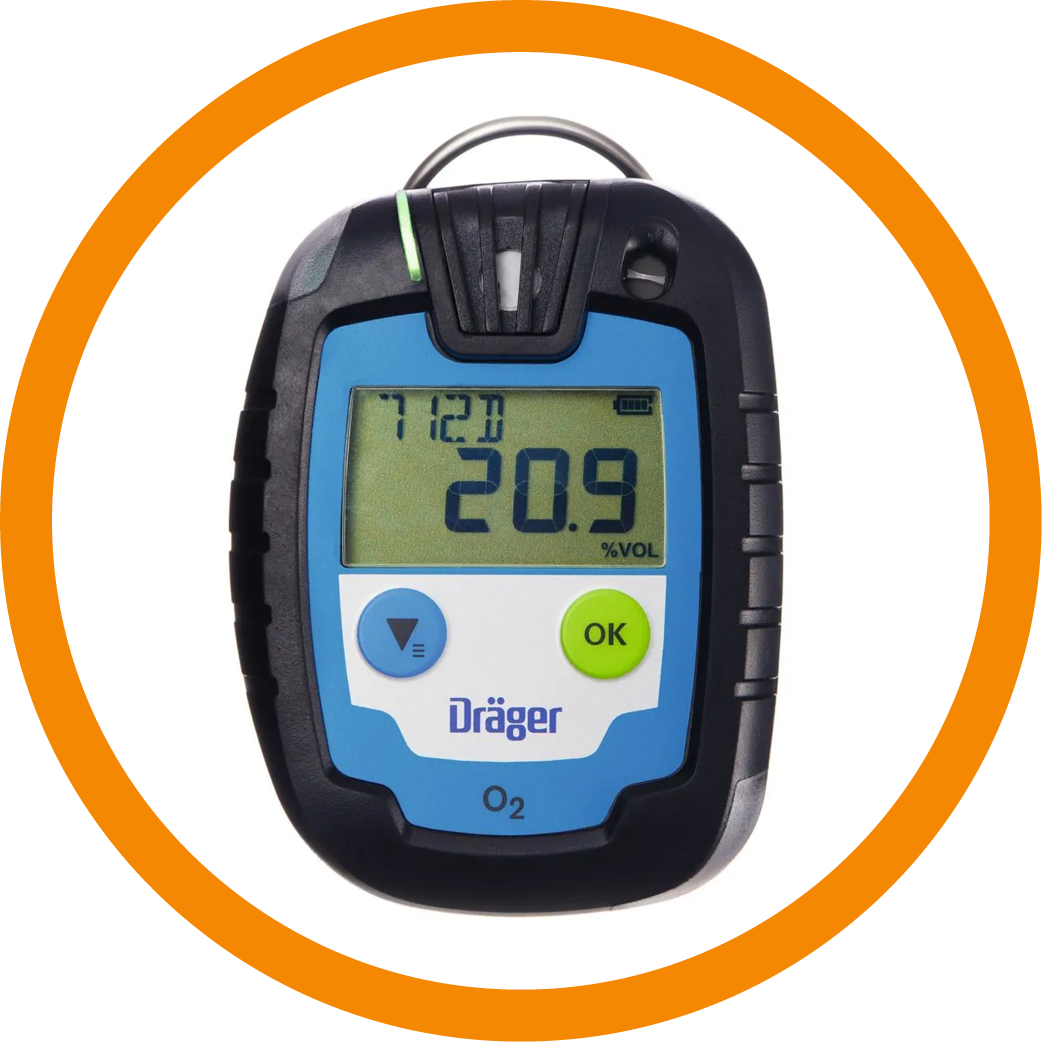
| Dräger Pac® 6500The Dräger Pac® 6500 allows the same measurement data to then be easily transferred to a record keeping system via Bluetooth®, with the same fast sensor response and a long-lasting rechargeable battery. More about the range |
Crowcon Gasman monitors
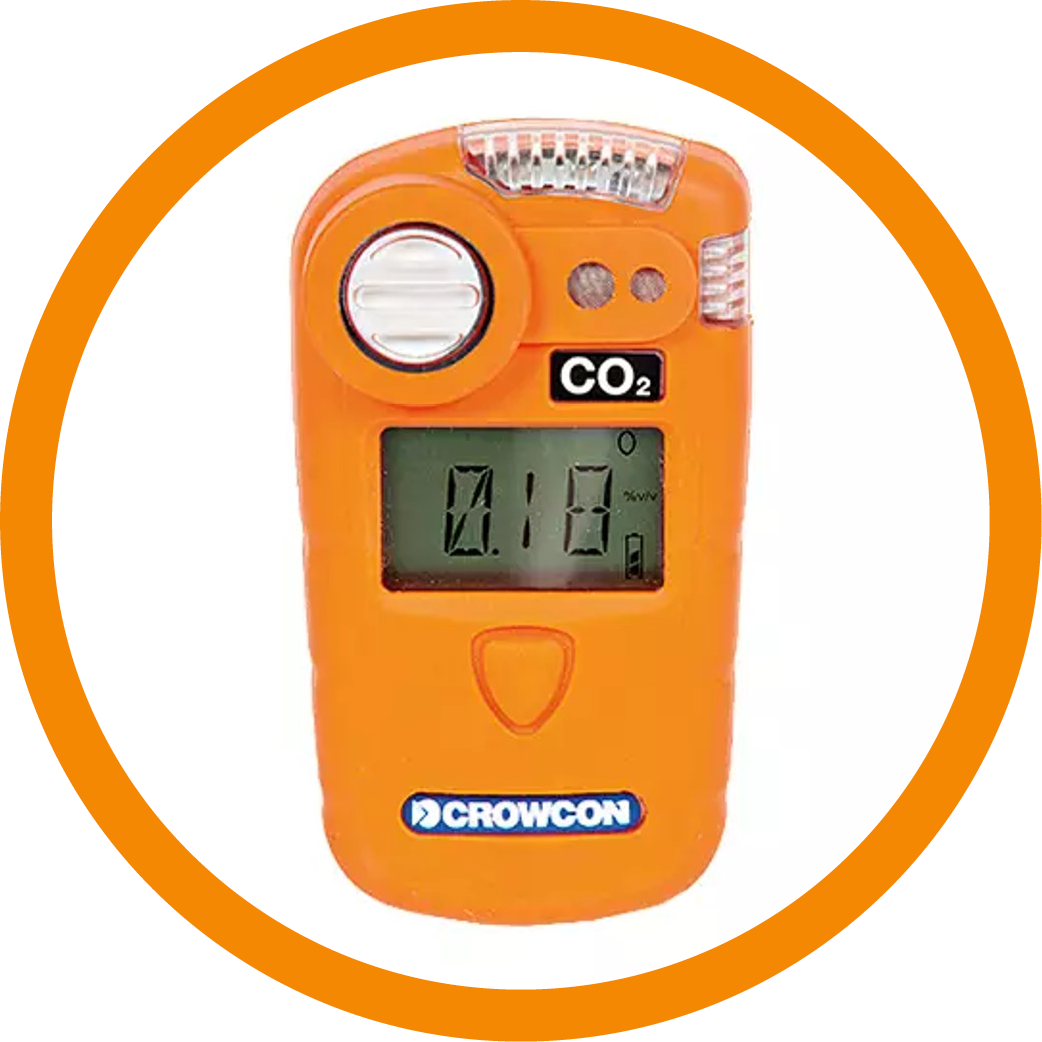
| Crowcon Gasman The Crowcon Gasman is an ultra-lightweight single gas detector, designed for use in the harshest of environments. Its compact and lightweight design makes it the ideal choice for industrial gas detection. Long lasting rechargeable lithium batteries and bluetooth capability make it a great choice for gas detection and compliance with HSE guidelines. More about the range |